ÇELİK
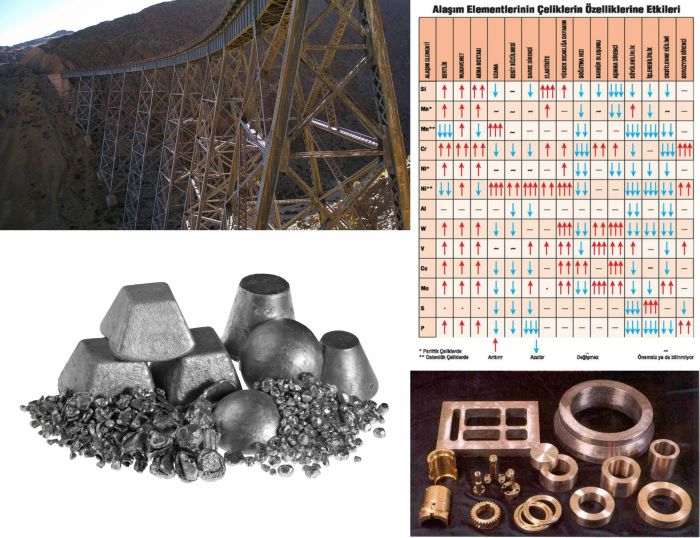
1. Metalürj. % 1,8'den az karbon içeren demir ve karbon alaşımı; mekanik ve ısıl işlemlerle çok çeşitli özellikler kazanabilir.| Kaba çelik, çelik ile dökmedemir arasında bir ara madde bileşimi taşıyan, karbon bakımından zengin çelik. || Özel çelik, olağan çeliğin düşük oranlarda taşıdığı elementlerden başka, bir ya da birçok katkı elementi içeren çelik. (Alaşımlı çelik de denir.) || Silisyumlu ve manganezli çelik, karbon ve özellikle silisyum oranı (% 1,30 ile 2) yüksek, manganez oranı % 0,75 olan makine yapım ve imalat çeliği. (Esneklik sınırı ve sertliği yüksek olan bu çelikler, tarım makinelerinin diskleri ve frezeleri, beton kırıcı vb. gibi darbe ve aşınmaya dayanması gereken parçaların, ayrıca yorulmaya karşı dayanıklığı nedeniyle lamalı yayların yapımında kullanılır.)
Sponsorlu Bağlantılar
3. ANSIKL. Cev. hazl. Çağdaş çelik fabrikalarının ayırtedici özellikleri şunlardır: oksijenle işleme yöntemlerinin ağır basması; elektrikle çalışan fırınların gelişimi; entegre sürekli döküm sisteminin kullanımı; izabe yöntemlerinin otomatikleşmesi sonucu üretim kapasitesinin artışı. Çelik fabrikalarında kullanılan yöntemler, özellikle dökme demiri çeliğe dönüştürmeye dayanır; dökme demir ise zengin cevherlerin kullanımıyla verimi artan yüksek fırınlardan elde edilir.
Çelik imalathanelerinin ayırtedici özelliklerini aşağıdaki özel işlevler oluşturur:
— beton çeliği, filmaşin, küçük profiller gibi tüketimi büyük boyutlara ulaşan ürünlerden özel ve sınırlı bir dizinin yerinde üretim ve pazarlanması;
— yerel hurda kaynaklarının değerlendirilmesi; artıkları azaltmak için hurdaya, önceden indirgenmiş topaklar katılır;
— bir santral yakınında uygun fiyatlarla elektrik kullanımı;
— değişik işlere yatkın niteliksiz yerel iş-gücünden esnek ve uyarlanabilir çalışma saatleriyle yararlanma.
Çelik imalathaneleri müşterilerle doğrudan ilişkiye girdiğinde, rekabet gücü yüksektir; yalın, dinamik ve çeşitli işlere uyarlanabilen yapısı vardır; üstelik sabit ve genel giderleri azdır. Genellikle donanımları şunlardır: çok yüksek güçlü elektrik fırını; sürekli ara ürün (kütük) döküm tesisi; basit ama üretkenliği yüksek çekme tezgâhları.
Ürüne ve pazara göre yılda 100 000 ile 600 000 t arasında üretim yapabilir.
4. Metalürj. Bozulabilirliği ve düşük mekanik dayanımı yüzünden demir, sanayide artık kullanılmamaktadır; oysa karbonla yaptığı alaşımlar en çok yararlanılan metalürji ürünleridir: yassılaşabilir ve dayanıklı çelik (karbon oranı °/o 1,8’den düşük); kırılgan olan, ama kolay kalıplanabilen dökme demir (karbon oranı % 2 ile 4).
ÇELİĞİN ELDE EDİLİŞİ
Günümüzde çelik, karbon giderme yoluyla dökme demirden elde edilir. Aynı zamanda kükürt ve fosforu olabildiğince giderilir ve diğer elementlerin (Si, Mn) oranı değiştirilir. Eskiden demir cevheri doğrudan doğruya çeliğe dönüştürülüyordu. Odun kömürüyle indirgenen cevher, arı olmayan dökme demir vermekteydi; bu ürün aygıtın en sıcak bölümünde, yani ha
vanın geldiği bölümde çeliğe dönüşüyordu (katalan ocakları). Aygıtın boyutları yavaş yavaş büyütülerek üretim artırıldı, ama sonradan yalnızca dökme demir üretiminde kullanılmaya başlandı (yüksek fırın); dökme demirin ise bir başka aygıtta (yer ocağı, günümüzde konverter ve elektrik fırını) karbon giderme işleminden geçirilmesi zorunluydu.
Birçok yöntem (Höganâs, Norsk-Staal, Krupp-Renn vb.) dökme demirden geçmeden, doğrudan doğruya cevherden demir ve çelik elde etme olanağı verir. Ne var ki, bu yöntemlerin gelişimleri çok sınırlıdır.
Çeliğin en yaygın üretim yöntemi sıvı arıtma'dır ve kullanılan çeliğin hemen hemen tümü bu yolla üretilir; işlem sonunda metal sıvı halde elde edilir.
Havayla arıtma.
(Bessemer ve Thomas konverteri). Bu yöntemler günümüzde ortadan kalkmak üzeredir; ancak geçmişte çok önemli bir rol oynamıştır. Bu yöntemde, karıştırıcıdan gelen sıvı dökme demir, konvertere boşaltılır ve aygıtın altından yoğun bir hava akımı geçirilerek metaldeki yabancı maddeler yakılır. Bu yanma, banyo sıcaklğın, dökme demirin erime sıcaklığından (1200°C)çeliğın erime sıcaklığına (1 600°C)değin yükseltmek için gereken ısıyı sağlar.
Asit ya da Bassemer yöntemiyle fosforlu olmayan ve silisyumca zengin (°/o 1,5 ile 2) dökme demirler işlenebilir; bu yöntemde konverterin astarı silis kökenlidir. Bazik ya da Thomas yönteminde ise çok az silisyum içeren (% 0,4 ile 0,6), fosforlu (°/o 1,7 ile 2) dökme demirleri işleme olanağı vardır; bu yöntemde konverterin astarı dolomit kökenlidir ve aygıta dökme demirle birlikte, fosforun giderilmesini sağlayan bir miktar kireç yüklenir. Dönüştürme işlemi çok kısa sürer(on beş ile yirmi dakika) ve dört döneme ayrılır: kıvılcım, alev, duman, arıtma. Katışkıların yükseltgenmesi silisyum ve manganezle başlar ve banyo üstünde yüzen bir arıtma cürufu verir (kıvılcım dönemi). Sonra karbon, havada büyük alevler çıkararak yanan (alev dönemi) karbonmonoksidi oluşturur. Duman dönemi (demir ve manganez oksidin kahverengi dumanları), Bessemer yönteminde kar bon giderme işleminin sonuna denk düşer. Thomas yönteminde ise bu dönem karbon giderme işleminin sonunda başlar ve özellikle fosfor giderme işlemini karşılar; fosfor giderme hava akımı kuvvetlendirilerek sağlanır (bu işlemin, karbon tümüyle yandıktan sonra başladığını belirtmek gerekir). Dönüştürmenin tamamlanıp tamamlanmadığını denetlemek için ya duman ve alevler incelenir ya da sıvı metalden alınan örnek levha biçiminde dökülür; bu levhalar hızla soğutularak kırılır; kırık yüzeylerin görünümü elde edilen ürün üstüne gereken bilgiyi verir. Son arıtmada gerekli katkılar sağlandıktan sonra konverter gövdesi yatırılarak çelik, bir potaya boşaltılır Thomas yönteminde, arıtmadan önce cüruf ayırma işlemi yapılır ve fosforca zengin arıtma cürufları toplanıp tarımda gübre olarak kullanılır.
Diğer yöntemlerde dökme demire uygulanan önarıtma ve ardından özel izabe cüruflarıyla son arıtma, kükürt ve fosfor oranlarının düşürülmesini sağlar.
Oksijen yöntemi.
Thomas ve Bessemer çeliklerinin kalitesini yükseltmek ve azotun zararlı etkilerini sınırlayarak, bunları Siemens-Martin ve elektrik fırınında hazırlanmış çeliklerin kalitesine yaklaştırmak için çelik uzmanları, klasik yöntemlerle oksijence zenginleştirilmiş hava üflerler. Çeşitli yöntemlerde arı oksijen kullanılır ve konverter çeliği denilen ürün elde edilir. Bunlar, Thomas ya da Bessemer dönüştürme yöntemleri ile Siemens-Martin fırınında işleme yöntemine karşı üstünlük sağlar.
Oksijen yöntemlerinin, klasik havayla dönüştürme yöntemlerine göre üstünlükleri şunlardır:
—yüksek üretkenlik ve 60 t yerine 300 t maksimum sığalı konverterlerin kullanımı sonucu saat başına üretim artışı;
—azot oranı 30 p.p.m’nin (milyonda bir) altında olan (bu oran Thomas çeliğinde yaklaşık 120 p.p.m. Martin çeliğinde 50
p.p.m’dir) yüksek arılıkta çelik üretme; bu çeliklerin biçim değiştirme (çekme sacları) ve kaynakla yapılan üretim alanlarında kulanılması salık verilir;
—hava üfleme yönteminde, azotun yol açtığı büyük kalori yitiminin ortadan kalkması, böylece karbonun, fosforun, manganezin ve silisyumun, banyoyu sıvı halde tutmaya yetecek ölçüde yanması;
—karbon oranı daha yüksek, yani °/o 0,4’ün üzerinde olan çeliklerin daha kolay elde edilmesi;
—hurda demir kullanımıyla sağlanan ekonomi;
—dumanın tozunu daha iyi giderme ve sürüklenen ürünleri geri kazanma olanağı.
Bu yönteme uygun ilk tesisat 1952’de Avusturya'nın Linz kentindeki Vöest çelik 'fabrikalarında kuruldu; o günden bu yana çeşitli yöntemler bulundu ve yavaş yavaş klasik yöntemlerin yerini aldı.
LD (Linz-Donawitz) yöntemi.
Oksijeni boruyla üfleme yöntemi Yukarı Avusturya'da Linz çelik fabrikalarında ve Steiermark bölgesinde Leoben'deki Donawitz fabrikasında uygulandı. Bu yöntem % 0,2 ile 0,4 arasında fosfor içeren dökme demirleri işleme olanağı verir; bu fosfor oranı, Bessemer yöntemi için çok yüksek, Thomas yöntemi için yetersizdir. En az % 98 oranında arı oksijen, dibi dolu dönüştürücü içine 10 barlık basınç altında, su dolaşımıyla soğutulan bir boruyla üflenir Oksijen, erimiş dökme demir banyosunun yüzeyine gelerek bir burgaç doğurur ve banyoyu karıştırır; böylece dökme demirin karbonunu gidererek çeliğe dönüşmesini sağlar. Elde edilen çeliğin kalitesi en iyi Martin çeliklerine eşdeğer ya da onlardan daha yüksektir. Buna karşılık işlemin, Bessemer ya da Thomas yöntemlerine göre biraz daha uzun sürmesi bir yana, ateşe dayanıklı astar iki kez daha kısa sürede bozulur. Öte yandan gerekli yatırım Bessemer ve Thomas yöntemlerine göre çok büyük boyutlara ulaşır; ayrıca bu yöntem bir toz giderme tesisinin kurulmasını zorunlu kılar.
LD Pompey yöntemi.
Yukarıdaki yöntemden türeyen bu yöntem, 1956'da Pompey çelik fabrikalarında uygulandı. Fosforlu dökme demiri işlemek için kullanılan bu yöntemde, bir yandan boruyla arı oksijen üflenir, öte yandan banyo yüzeyine yayılan tane biçiminde kireç katılarak zenginleştirilmiş bir izabe cürufu kullanılır, işlem iki evrede gerçekleşir: birinci evrede fosfor oranı çok büyük ölçüde düşer ve fosforla yüklü izabe cürufu gübre olarak kullanılır; ikinci evrede arıtma son bulur ve 5 bu işlem sonucu oluşmuş izabe cürufundan daha sonra doldurulan dökme demir yükünün fosforunu gidermede yararlanılir.
Kaldo yöntemi.
Profesör Kalling’in Domnarvet’te (İsveç) incelediği bu yöntem (adı buradan gelir), LD yöntemi uygulanamayacak ölçüde fosfor içeren dökme demirler için kullanılır; bilindiği gibi LD yönteminde en çok °/o 0,5 oranında fosfor içeren dökme demirler işlenebilir. Kaldo yönteminin ayırtedici özelliği, dibi dolu, eğik, salınımlı ve döner (30 dev/dk) bir konverter gövdesinden yararlanmasıdır; arı oksijen 4 barlık basınçla yüzeye üflenir. Birçok cüruf ayırma işleminden sonra, işleme koşullan (konverter gövdesinin dönme hızı, oksijen debisi) ve karbon giderme İşlemi, fosfor gidermeye göre ayarlanabilir; yani fosfor oranını çok düşük bir düzeye indirerek ekonomik koşullarla yüksek arılıkta çelikler elde edilebilir. Bu yöntemin temel özelliği, artık kalori sağlayarak ton başına 400 kg'a kadar hurda katma olanağı vermesidir; bu olgu, banyoyu sıvı halde tutmak için gerekli ısıyı yalnızca banyo içi tepkimeyle sağlayan yöntemlerde önemli bir gelişmedir.
Rotor yöntemi.
Almanya'da Oberhausen' de uygulanan bu yöntem, Siemens-Martin fırınında işleme ile konverter gövdesinde işleme arasında bir ara yoldur; yatay eksenli çok uzun (20 ile 30 m) bir fırın kullanılır; fırın çok yavaş dönerken (0,5 ile 1 dev/dk) erimiş dökme demir banyosuna oksijen iki tüyerli bir boruyla verilir: tüyerlerden birinden arı oksijen gelerek banyo içine dalar ve karbonmonoksit oluşturur; diğeri oksijen oranı °/o 75 olan havayı banyo yüzeyine üfleyerek karbonmonoksiti yakar. Bu yöntemin sakıncalarından biri, ateşe dayanıklı astara zarar verecek ölçüde ısı açığa çıkarmasıdır.
OLP (oxygene-lance-poudre) [oksijen-boru-toz] yöntemi.
Demir çelik sanayisi araştırma enstitüsü’nce incelenen bu yöntem fosforlu dökme demirlerin arıtılmasında kullanılır; bu yöntemde tabanı dolu bir konverter gövdesinde, düşey bir boruyla ye oksijenle birlikte toz kireç püskürtülür. Üfleme işlemi iki evrede uygulanır: ara cüruf ayırma; hurda ve cevher katma; böylece elementlerin oranını ayarlamada daha yüksek bir esneklik sağlanır. Fransa'nın doğusunda fosforlu dökme demirleri işlemede kullanılan bu yöntem çok yüksek tesisler gerektirir. Dolayısıyla yerini Çelik sanayisi araştırma enstitüsü ile VVendel -Sidelor'un ortaklaşa geliştirdiği LWS yöntemine bırakma eğilimi vardır; LWS yöntemi tabandan bir oksijen-hidrokarbon karışımı vermeye dayanır (hidrokarbonun ısıalan krakingi pota tabanının soğumasını sağlar).
Siemens-Martin fırınında arıtma.
Konverterlerde olduğu gibi Siemens-Martin fırınlarının da asidik ve bazik olanları vardır. Asidik Siemens-Martin fırınında yalnızca karbon, silisyum ve manganez arıtması yapılır, kükürt ve fosfor aynen kalır; bazik Siemens-Martin fırınında ise diğerleriyle tyrlikte bu iki element de ayrılır. Thomas ve Bessemer yöntemleri gibi Siemens -Martin fırınında arıtma yöntemi de kaybolmaya yüz tutmuş ve yerini elektrik fırını almıştır.
Elektrik fırınında arıtma.
Bu yöntem metalin çok yüksek derecede arıtımını sağlar. Gerekli ısı karbon elektrotlar ile fırına doldurulmuş gereç arasında oluşturulan arkla elde edilir.
Erimeden sonra arıtma, çeşitli izabe cürufları katılarak gerçekleştirilir. Bazik yöntemde, yükseltgen bir izabe cürufuyla silisyum, manganez ve karbon giderilir; banyonun fosforunu elemede ise aşırı bazik ikinci bir izabe cürufu kullanılır. Cüruf ayırma işleminden sonra indirgen ve bazik bir izabe cürufuyla oksit ve kükürt elenir. Ardından, istenen bileşimde çelik elde etmek için son katkılar eklenir.
Öte yandan elektrik fırınında, konverterden gelen sıvı yükler işlenerek de son arıtma uygulanabilir (Dupleks yöntemi); bu tür uygulamada elektrik akımı tüketimi çok düşer.
Elektrik fırınında yükseltgeme döneminde oksijen kullanılır; böylece tepkimelerin daha hızlı ve daha iyi gelişimi sağlanır. Çelik üretiminde kullanılan ve indüklemeyle ısıtılan bir diğer tür elektrik fırını da vardır. Ne var ki indükleme yöntemi ileri ölçüde arı yük gerektirir ve yalnızca, özel element oranı yüksek çok arı çelikler elde etmek için kullanılır.
Bu alanda, özellikle "çok yüksek güçte" yeni tip ark fırınlarıyla önemli gelişmeler sağlandı. Yeni fırınların özgül gücü 1 ton çelik başına 500 kVA’e ve günümüzde kullanılan sığaları 100 t'a, hatta kimi kez 400 t'a ulaşır; oysa klasik ark fırınlarında güç 200 kVA ve sığa 40 t'dur. Ayrıca harcanabilir elektrotlu özel bir ark fırınında elektrik ileten izabe cüruflarıyla çeliği yeniden eritme olanağı vardır; bu yöntem, arı ve özel çelik elde etmede kullanılan, vakum altında arkla yeniden eritme yöntemiyle yarış halindedir.
Potada hazırlama
indükleme fırınında olduğu gibi bu yöntemde de potada yalnız çok arı ürünler eritilir. Potalar, ya küçük kok fırınlarında ya da gaz ve fuel-oille çalışan ve artık ısı kazanma sistemi bulunan fırınlarda ısıtılır. Erimiş çelik elde etmede ilk kez bu yöntem uygulanmış ve uzun süre kullanılmıştır.
Kaynak: Büyük Larousse
Son düzenleyen Safi; 9 Temmuz 2016 06:40
Tanrı varsa eğer, ruhumu kutsasın... Ruhum varsa eğer!